The building stock and construction sector are responsible for a considerable share of greenhouse gas emissions and material waste, demanding immediate action to revert these scenarios. Making the European construction sector more sustainable can help reduce 42% of final energy consumption, 35% of greenhouse-gas emissions, 50% of extracted materials, and up to 30% of water consumption [1]. In The Netherlands, building materials account for 70% of the climate emissions from the building industry; construction and demolition account for 5% of the climate emission [2]. A promising approach is the use of renewable natural materials. They have the potential to be as durable, strong, and versatile as their conventional synthetic counterparts, but the range of choice is still narrow. Joining forces from different knowledge domains to experiment and prototype is utterly important to develop, promote, and popularise innovative alternatives along the entire value chain.
"When combined, they can create a fully natural material with similar characteristics to timber"
Wood is typically a well-recognized option by society, and the widely available processed timber presents remarkable properties. However, its use comes with drawbacks related to excessive waste from conventional subtractive fabrication processes, need of adhesives (which are often toxic or based on fossil resources), and difficulties in the fabrication of complex geometries. The strength of wood derives from its building blocks (lignocellulosic fibres), which are the most abundant biopolymers in nature [3,4]. Cellulose is commonly used as raw material in the paper industry and as a fibre reinforcement on bio-based composite. Lignin is a by-product from the same industry, usually burnt as an energy source; recently increasingly recognised as renewable resources [5,6,7,8]. They can be extracted from several waste streams, including agricultural and forestry waste. When combined, they can create a fully natural material with similar characteristics to timber but with potentially adjustable mechanical properties and more freedom to generate complex structures.
The on-going Wood Without Trees project studies a solution to upcycle both components into a fully biobased material for additive manufacturing. The project aims to be a stepping stone towards full circularity (from locally sourced bio-waste streams to material recyclability within the construction industry), while allowing for easy-to-tune material properties and high-performance building components thanks to 3D printing – and thereby resulting in reduced greenhouse gases emissions and waste.
The project develops material mixtures, involving knowledge on biobased resources and chemical processes from Wageningen Food & Biobased Research. Experts from TU Delft Aerospace Structures and Materials provide further knowledge on bioinspired materials and polymer science. The mixtures are defined in function of properties required in the building industry, with inputs from TU Delft experts in Structural Design & Mechanics and Design of Construction. The mixtures and the 3D printing process are intertwined, based on knowledge in digital fabrication from TU Delft Design Informatics experts at the Laboratory for Additive Manufacturing in Architecture (LAMA). At LAMA, the 3D printed samples are being produced for different mixtures by the researchers, integrating inputs from the various knowledge domains. The team gathers regularly for interdisciplinary brainstorming. Besides sharing knowledge, also sharing facilities (e.g. TU Delft laboratories for aerospace, civil engineering, and architecture) is a pillar in the collaboration, which overcomes disciplinary boundaries and gives concrete ground to cross-fertilisation and knowledge-exchange across domains. The mixtures are produced with equipment from TU Delft laboratories at Aerospace Engineering; the 3D printed samples are tested in several TU Delft laboratories to study the properties of the 3D printed material, showing promising results so far. The resulting knowledge is being used by the SME Liebrand Holding BV to define the “recipe” and production process of the final material. Liebrand pioneered this project with his graduation thesis in Building Technology at TU Delft in 2018 and is pursuing a commercial use. The collaboration also generates a novel network between TU Delft Faculty of Architecture and the Built Environment, the Faculty of Aerospace Engineering and Wageningen UR Lignin Platform, bridged by an innovative SME for bio-materials toward market applications.
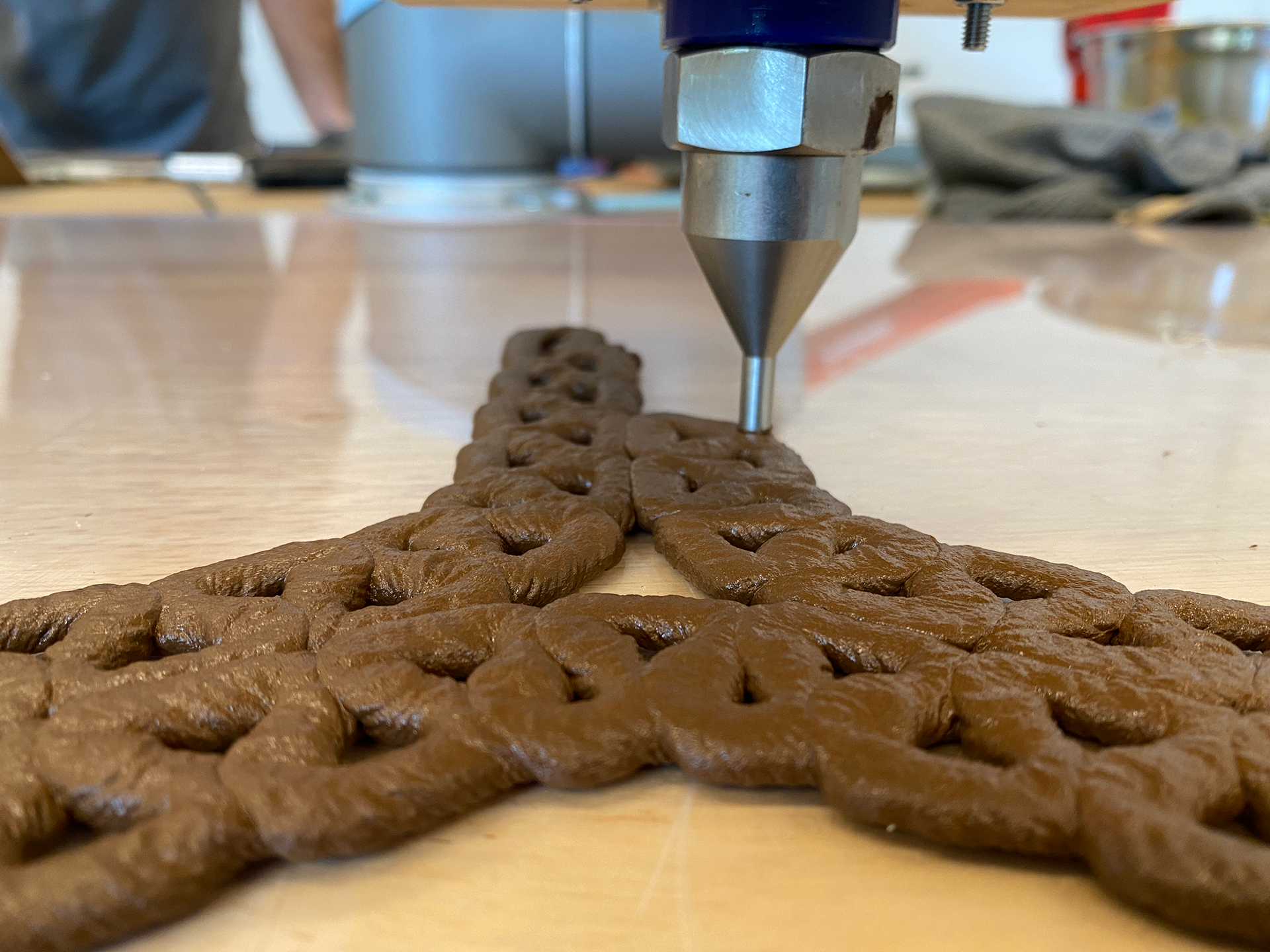
"This project intends to trigger a paradigm shift along the value chain towards sustainability of the built environment."
This project intends to trigger a paradigm shift along the value chain towards sustainability of the built environment. The scientific knowledge generated in this project paves the road for a “liquid wood” bio-based material sourced from agricultural and industrial residues, to be used for optimised building components – for which the involvement of wood producers and building constructors among other targeted stakeholders is soon needed to facilitate the creation of social-economic values. Similarly, stakeholders on management of agricultural and forestry bio-waste and residuals are needed about lignin and cellulose processed from agricultural and forestry feedstock and residual streams. The impact could be increased with involvement of policy makers for circularity, to gain understanding of business models with legal perspectives and incentives to users, toward large scale applicability - as the value chain established with the upcycling of residues from different industries and the potential of creating a full-circular production process suggests innovation in the business models.